This article presents a study of the conventional sandwich plate designs subjected to blast loads. In the conventional sandwich design consists of thin outer (loaded side) and inner facesheets made of fibrous laminates, separated by a layer of structural foam core. Two models’ facesheet materials are (1). (0/±45/90)s Carbon/epoxy (2).Steel. Comparisons of the two models are made during a long time period of 5.0 ms, initiated by a pressure impulse lasting 0.05 ms applied to a single span of a continuous plate. In the initial response phase the overall deflections are limited and considerable foam core crushing is caused in the 1st design by the incident compression wave. This type of damage is much reduced in the model (2) with Steel facesheet which leads to significant reductions in facesheet strains and overall deflection. The total kinetic energy of the model (2) with steel is much lower than that of a Carbon/epoxy plate, and so is the stored and dissipated internal energy.
Introduction
A sandwich structured composite is a special class of composite materials that is fabricated by attaching two thin but stiff skins to a lightweight but thick core. The core material is normally low strength material, but its higher thickness provides the sandwich composite with high bending stiffness with overall low density.
Open and closed cell structured foam, balsa wood and syntactic foam, and composite honeycomb are commonly used core materials. Glass or carbon fiber reinforced laminates are widely used as skin materials. Sheet metal like steel is also used as skin materials in some cases.
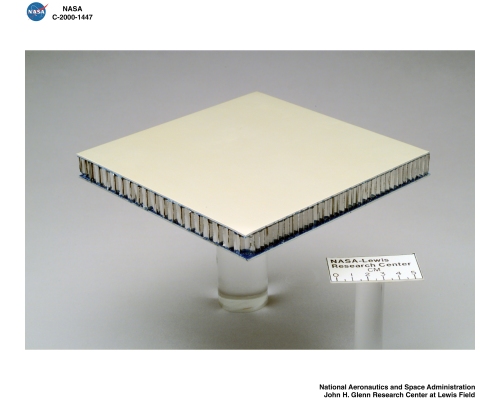
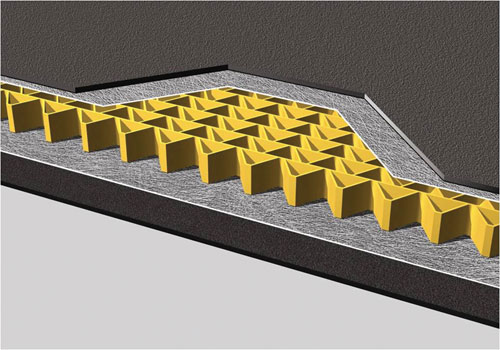
Fig. 1 Sandwich Plate
Designs, material properties and loads
A multi-span sandwich plate supported by equally spaced rigid stiffeners is used. And it has assumptions as follows:
- The connections between the different layers are perfect.
- Assume moisture and temperature effects as zero.
- Assume voids in the composite are zero.
The length of the plate is L=1000 mm. The length of a single span between supports is L’= 600 mm. The total width, measured in the X2-direction of Fig. 2 is assumed to be sufficiently large, so that the plate can be analyzed in plane strain, with displacements u2 = 0 everywhere. Width of the supporting stiffeners is d = 100 mm, such that the clear span of the sandwich plate is L-d = 400 mm.
Continue reading ‘How to establish a sandwich plate in Hypermesh (I)’